Our slitting department is equipped with a variety of different slitting machines. The classic type of film slitting in the film processing industry is roll slitting. Different slitting techniques are used depending on the material, roll length, slitting width and quantity. Among other things, papers, films and nonwovens can be processed to customer specifications. It is advisable to first carry out a cutting test on products provided by the customer.
For standard materials such as
-
Polyester films
-
Kapton films
-
Glass fabric
-
Nominal papers
has many years of processing experience.
Slitting is at the end of the value chain in the production and processing of web materials . Very often, the large rolls ("jumbo rolls, master rolls") from the coating process are converted to smaller formats (pre-cutting). In addition, the preparation of so-called log rolls (large width but defined, short running length) can also take place as a production step before slitting. The final step is the production of customer-specific slit rolls in almost any width (1/10 mm pitch) or further processing as punched parts.
Conditions for contract work
- The cutting widths are between (1 mm) 3 mm - 1,500 mm, in 1/10 mm increments
- The roll length can be between 5 m and up to 2,500 m (maximum outer diameter must be observed)
- Standard tolerance +/- 0.2 mm (greater accuracy is possible if required)
- The film thickness can range from 0.012 - approx. 0.500 mm (up to 3 mm depending on the material)
For further details, please refer to our general conditions for contract work
Roll slitting
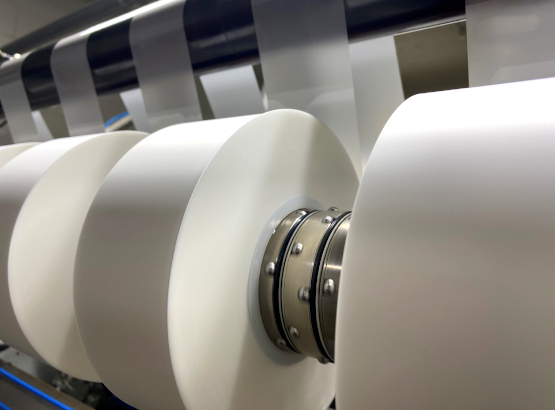
This process is the classic type of film cutting in the film processing industry. It involves working from the roll onto the roll, i.e. the material is unwound and fed through a rotating set of blades (shear cut). The individual cut rolls are then rewound alternately on two separate axes. The shear cut can cause deformation at the edge of metal foils, for example (material displacement). However, this effect can be counteracted with special knife sets.
The slitting process (also known as winding slitting or rewinding slitting) is usually used when large quantities of uniformly wide rolls need to be produced.
Format cutting - Sheet formats
During slitting, the web-shaped roll goods are cut to a customer-specific format (sheets) and no longer wound up. Slitting thus also forms the transition to the production of individual die-cut parts and labels.
No cutting in the sense of the processes described above. Rather, the very long jumbo rolls, for example, are cut to a shorter length by cutting at right angles to the direction of the web. Finally, in format slitting, the web-shaped goods are cut to a customer-specific format (sheets) and are no longer wound up. Format slitting thus also forms the transition to the production of individual die-cut parts and labels.
The maximum format size is 2,500 x 2,000 mm with low tolerances (larger formats on request). Of course, smaller formats are also possible. Material thicknesses up to 5 mm.
Parting off
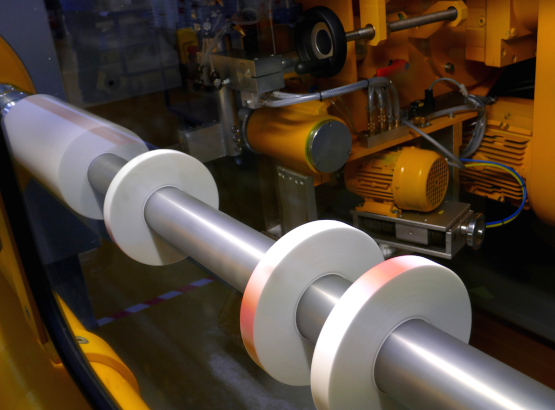
The log rolls (large width rolls already cut to the correct length, e.g. 66 m) are placed on a rotating axle and cut to the desired width by a tangentially dipping, rotating knife. The displacement by the plunging knife material and the unavoidable heating due to friction (cooling e.g. with water) set limits to the process.
However, the great flexibility and very fast individualization of the cutting width are advantageous, which is particularly important for frequently changing customer orders. This technology is therefore likely to be used even more in the future to better adapt to customer requirements.
Laminating
During formatting or independently of it in advance, different products can also be combined by laminating. Some of the laminators used are specialized in laminating very thin films in the single-digit micrometre range (>6µm depending on material strength).
The technology used for this is very complex so that the laminates can be produced without distortion.