partial discharge resistant adhesive tapes
Steigende Betriebsspannungen erfordern bessere Isolationsmaterialien.
With the increasing demands on insulating materials, particularly in electromobility and renewable energies, partial discharge resistance (PD resistance) is becoming more and more important. But what exactly is behind partial discharge and why are materials such as Kapton® CR the solution?
Kapton® CR is characterized by exceptional resistance to corona and partial discharge - a decisive advantage in demanding applications where high voltages and long service lives are required. This material is the ideal choice for electromobility, wind power and solar systems and high-voltage motors in particular.
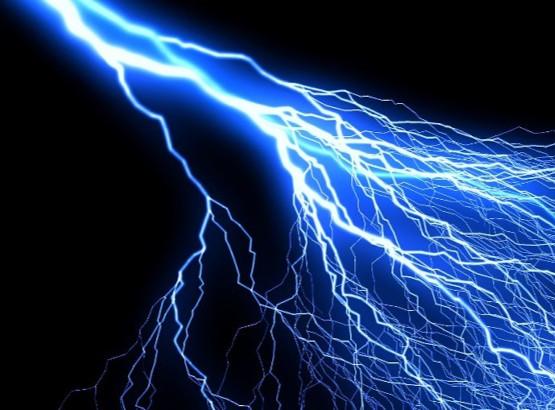
what are partial discharges?
Electrical partial discharges are localized electrical discharges that occur on the surface of insulating materials or in defects within insulating materials when the electric field strength becomes too high at certain points. The voltage discharges do not penetrate the entire insulation section. The partial discharges generate heat, UV radiation and ozone, among other things. Sooner or later, an organic insulating material is damaged and a conductive path is formed. At a later stage, this damage ultimately leads to a full breakdown and thus to a short circuit.
Kapton® CR
Even inert polymers such as PTFE are gradually damaged by partial discharge phenomena. Only inorganic products are resistant to corona (e.g. glass, ceramics, mica). This property is utilized in the polyimide film Kapton® CR. Due to an admixture of inorganic components, it exhibits exceptional resistance to corona and partial discharge.
Challenges and solutions
For demanding applications, such as frequency converters in wind power and solar systems (690 V to over 1000 V operating voltage), but above all in electromobility, cheaper insulation films such as polyester or PEN are often not sufficient. Additional degradation and ageing processes (e.g. hydrolysis) can impair the insulation performance, particularly in the presence of moisture and heat.
Kapton® CR has long been used in high-voltage motors and generators. Studies by ABB and Siemens have shown that the glow discharge resistance of Kapton® CR is significantly higher than that of conventional Kapton® HN or polyimide films from other manufacturers. This is particularly important, as above a certain size of electrical machine or transformer, partial discharge can no longer be avoided with reasonable effort.
In contrast to fluoropolymer films, which are also more resistant to glow discharge, Kapton® CR does not tend to yield under pressure (cold flow). The dielectric strength is not reduced by a change in thickness. In addition, Kapton® CR is easier to process than mica-coated fabric tapes and has a significantly higher dielectric strength than aramid papers with a high mica content.
Conclusion
If high voltage, environmental influences and a long service life are required, it makes sense to use the special Kapton® CR insulating films. The self-adhesive, corona-resistant polyimide films from CMC Klebetechnik are the first choice for modern long-term requirements (>>10,000 hours) or particularly stressful high-voltage applications (e.g. electromobility at 900 V).